High end selective soldering system to integrate into lean-manufacturing concepts (U-Shape)
Mini-wave soldering for high flexibility or multi-wave soldering for high volume-applications
Product change without loss of production time even for multi-wave processes
Parallel process through separation of fluxing, preheating and soldering
Use of up to 4 flux spray heads
Up to 2 lower preheaters with optional upper convection preheater
Ideal for linking with manual work stations and peripherals
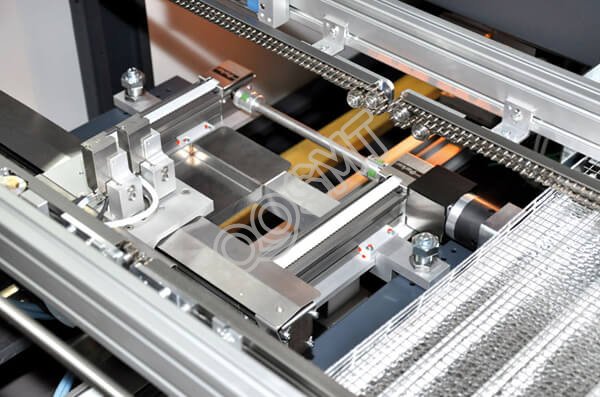
Ersa ECOCELL
Predestined for production in manufacturing islands
With the Ersa ECOCELL, the worldwide technology leader in selective soldering systems expands his product range with a system that fully responds to the demands of modern production methods. The ECOCELL works according to the Toyota principle, and conveys the PCBs in the counterclockwise direction. This U-shaped arrangement makes the system ideal for use as part of a production island, but it can also be operated as a "side-line".
Simultaneously processing up to 4 PCBs
The notions of high throughput and high flexibility, mentioned together in one sentence, are not contradictory to each other. With 2 integrated preheaters, up to 4 printed circuits boards can be processed simultaneously. Dual pot systems open up the possibility to efficiently solder multiple up panels. And equally, when using mini-wave and multi-wave systems, different solder alloys can be handled.
This function, together with the possibility to service one multi-wave bath while the other one is in operation, reduces the tool change time during a product change to a minimum. The well proven spray fluxing unit is also installed in the ECOCELL. With the integrated flux spray control, flux deposition, whether in single points or in tracks, is performed on a high quality level. The short wave IR emitter cassettes, mounted on the lower side of the boards, can be optionally augmented with a top-side convection preheating unit, thereby assuring a homogeneous soak of even the most complex board assemblies. A further available, optional upper convection preheater unit over the mini-wave bath assures that the boards maintain the optimal process temperature for the duration of the solder process.
The "peel off" effect developed by Ersa for soldering at a 0° angle eliminates the risk of bridging and ensures achieving the lowest DPM rate. For the solder bath itself, only induction pumps are being deployed to pump the solder into the wave, which makes these pumps a low-maintenance and wear-part-free item. The intuitive system software allows effective programming of the system and records all production relevant data (traceability) as per ZVEI standard. The graphical interface of the CAD assistant permits quick and easy off-line programming while the system is in operation, thereby ensuring the maximum availability of the system for production.
Dimensions
Length from 2,600 mm
Width approx. 1,950 mm
Height approx. 1,600 mm
Conveyor support
Pin-and-chain conveyor for frameless PCB transport
PCB width: 63.5-356 mm
PCB length: 127-356 mm
Maximum PCB top side clearance: 120 mm
Maximumg PCB bottom side clearance: 60 mm (30 mm upto z – variable)
Maximum PCB weight: 8 kg (option 12 kg)
Media supply
Nitrogen
Pneumatic system
Electric supply
Extracted air
Flux module
Drop-Jet in different sizes
Preheat module
Dynamic IR heating, convection or combination of IR and convection
Solder module
Electromagnetic solder pot
Mini-wave 13 kg up to 2 pots
Multi-wave soldering area up to 356 x 356 mm
PCB size up to 406 x 508 mm
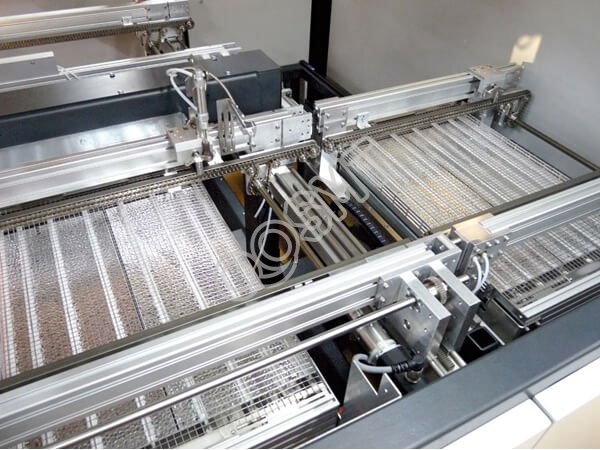
Options:
Roller and pin-chain conveyor for direct board handling
Programmable width adjustment
Precision Drop-Jet Fluxer, up to 4 spray head and 2 different flux media
Maximum permissible board weight: 12 kg
Spray jet control
Preheat individually configurable, IR emitters, convection on top and bottom side
Pyrometer to monitor temperature
2 solder bath for mini-wave applications
2 electromagnetic multi-dip bath
Tool-change "on the fly", rest-oxygen control in multi-dip tool
Take-over of board data from CAD system